Best Practices for Inventory Management
Learn the best practices for inventory management with this comprehensive guide and optimise your inventory management techniques for success.
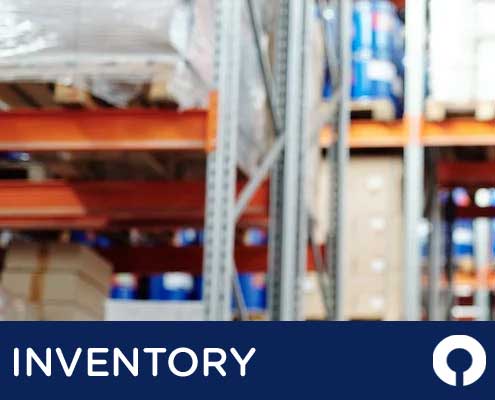
Learn the best practices for inventory management with this comprehensive guide and optimise your inventory management techniques for success.
Inventory management is no easy job. A business’ inventory is one of its most valuable assets and a great deal of your capital is likely tied up in it. Without airtight inventory management strategies you’re likely just throwing money down the drain.
Holding too much or too little stock is a recipe for disaster; lost shipments, incorrectly filled orders, poor organisation in the warehouse, expired or dead stock, and a wide range of other problems can be compounded when your inventory management practices are outdated and inefficient. This leads to wasted time and resources, disappointed customers, and damage to your brand’s reputation. It’s not ideal. Understand the difference between stocktaking and stock checking, and determining which one you need.
So, what can you do to improve and streamline management of your inventory? Here’s our guide to optimising your inventory management efforts.
Inventory management means all the processes involved in buying, manufacturing, storing, and selling your inventory. Inventory is classified as a current asset as it is usually intended to be sold within a year, and includes raw materials, work in progress parts, and the finished products ready for sale.
Two terms that are often confused, inventory management and inventory control have slightly different meanings that are important to clarify. While inventory management is the wider practice of forecasting and replenishing inventory, taking into account sales trends, tracking changes in supply chains, and more, inventory control (also called stock control) focuses on maintaining and optimising the stock levels that are currently in the warehouse. Inventory control can be seen as part of the wider inventory management strategy.
With effective inventory management, your business can save money by reducing losses on items that are lost or spoil while sitting in the warehouse. It helps you gain visibility over real-time sales patterns to help you order the right amount of stock at the right times and forecast future needs to ensure customers always get what they need. Moreover, effective inventory management techniques allow you to better utilise warehouse space and optimise operations, including for multi-location inventory. This means that your operations can run smoothly without error or delays.
To achieve these benefits, let’s take a look at some key inventory management techniques to implement.
It’s important to carry safety stock to ensure that there is always enough inventory to meet customer demand, even when unexpected events occur. This could include unexpected spikes in demand, delays in receiving new inventory, or unforeseen supply chain disruptions. Having additional stock allows you to safeguard against stock-outs and errors in inventory counting or forecasting, helping you avoid major issues and disappointed customers.
However, it’s critical that your organisation doesn’t carry too much stock. With too much stock you quickly accrue higher holding costs, insurance costs, and more. Demand for the items may fall or they may become obsolete, leaving your organisation with excess that must be disposed of. Moreover, there’s a higher risk of damage or theft when there’s too much stock in one location.
A key responsibility in inventory management, therefore, is finding the sweet spot of stock levels and implementing strategies to keep it at desired quantities. To do this, an ABC analysis can be useful…
An ABC analysis is an inventory management technique where you categorise items into three camps based on their value and sales frequency. This allows you to organise the warehouse to optimise how and where stock is stored. The categories are as follows:
High priority items that are sold in the largest quantities and need to be regularly reordered are considered A items in your inventory. These products often require constant reviews to ensure quality.
Medium priority products which need to be replenished once a month or so are considered B items in your inventory. These are still valuable but not as high priority as the A group.
Low value products that sell often and are replenished infrequently are considered C items.
There are two main methods of determining how and when to restock in inventory management: periodic review and continuous review. The type of business, products, and inventory flow will help determine which option is better for your organisation.
The periodic review inventory management system is where you order new products at regular intervals. By evaluating the inventory levels of each item at the end of the period you can determine how many new items to order. This means that the number of products ordered may change each time.
Instead of placing orders for new products after a predetermined interval, the continuous review system involves replenishing stock after the quantity of an item reaches a set level. With this system of inventory management, tracking quantity levels is essential. Usually, the same number of new products are ordered each time.
In summary, periodic review consists of ordering a different number of items after a set period of time, while continuous review means ordering the same number of items after stock levels dip to a certain point.
Strategically organising your warehouse is another best practice for inventory management. In addition to keeping the inventory neat and organised across your single stock room or multiple warehouses, creating a system for how inventory is stored can help streamline all processes.
The first in first out principle in inventory management is key for businesses selling products that are perishable or need to be rotated. By selling the oldest inventory first, you can minimise losses on spoiled stock, reducing wastage and saving money.
For the FIFO approach to work, it’s important to plan for stock rotation in the warehouse. The oldest stock (first in) should be located at the front of the warehouse so it can be sold fastest (first out), while newer stock is moved to the back of the warehouse.
Barcode tagging can help keep tabs on the flow of inventory around the warehouse with location tracking. Check out our guide to barcode asset tracking to find out more about how barcodes can help you with tracking inventory and assets in your warehouses.
Quality control is more than just occasionally checking products for problems such as signs of damage or missed expiration dates — it also means considering the warehouse environment and any ways that storage might impact the quality of products. For example, the temperature and humidity levels in the warehouse might impact products in storage, or light may damage them.
By implementing effective quality control procedures, businesses can reduce the likelihood of customers receiving defective or damaged inventory, which can lead to costly returns and delays in order fulfilment. Additionally, by ensuring that inventory meets quality standards, you can minimise the risk of stock-outs and increase the likelihood of repeat business from satisfied customers.
To improve quality control, first identify the key points in your inventory management process where quality control is most important. This could include points such as receiving, storage, picking, packing, and shipping. Then, develop procedures and checklists for each critical control point to ensure that quality standards are consistently met.
Inventory KPIs can help you measure the efficiency of your inventory management efforts. Some essential key performance indicators include cycle time, inventory write-off, carrying costs, fill rate, and order status and tracking. Tracking these KPIs is useful as this can help businesses to identify areas for improvement in their inventory management processes. By measuring KPIs over time, businesses can identify trends and patterns that may indicate inefficiencies or bottlenecks in their inventory management processes.
Furthermore, tracking KPIs such as carrying cost of inventory and days of inventory on hand, helps decision-makers better understand the costs associated with holding inventory and make informed decisions about optimal inventory levels.
To calculate when stock needs to be replenished, it’s useful to use the reorder point formula. The equation is:
Reorder point = (average daily unit sales x average lead time in days) + safety stock
Carrying safety stock is essential because this extra inventory protects you from market spikes and slumps, stock-outs, or changing lead times.
Calculating the rate of inventory turnover tells you how many times the inventory is sold in a set period such as a year. The formula for inventory turnover rate is:
Inventory turnover rate = cost of goods sold / average inventory
This calculation helps you evaluate demand for the items and plan how to increase the rate of turnover.
In 2023, practising inventory management manually in spreadsheets or using low quality software is akin to shooting yourself in the foot. To save time, avoid human errors, and gain real-time visibility over inventory, try FMIS stock and inventory management software.
Designed for any business with a large quantity of inventory, this powerful tool in the FMIS asset management repertoire can update stock levels in real time, automate reordering in line with your chosen system, increase warehouse efficiency, and decrease costs. Integrated barcode scanning makes completing warehouse audits a breeze while customisable automated workflows and approvals keep everything running smoothly.
Fully configurable for your needs, FMIS inventory and asset management software can be hosted in the cloud or on-premises. It’s ideal for engineering, procurement, and construction businesses or any organisation that wants to gain greater control over complex kitting and assembly processes.
Ready to see for yourself how stock and inventory management software can streamline your operations and benefit your bottom line? Book a free demo of FMIS asset management software today or get in touch to find out more.
For more information on how FMIS can help you effectively track and manage your assets and equipment, please get in touch with an FMIS consultant or call us on +44 (0) 1227 773003.
FMIS Ltd
167b John Wilson Business Park
Whitstable
Kent
CT5 3RA
United Kingdom
Phone:+44 (0) 1227 773003
Fax:+44 (0) 1227 773005
Sales:sales@fmis.co.uk
Support:support@fmis.co.uk
Cookie | Duration | Description |
---|---|---|
cookielawinfo-checkbox-advertisement | 1 year | Set by the GDPR Cookie Consent plugin, this cookie is used to record the user consent for the cookies in the "Advertisement" category . |
cookielawinfo-checkbox-analytics | 11 months | This cookie is set by GDPR Cookie Consent plugin. The cookie is used to store the user consent for the cookies in the category "Analytics". |
cookielawinfo-checkbox-functional | 11 months | The cookie is set by GDPR cookie consent to record the user consent for the cookies in the category "Functional". |
cookielawinfo-checkbox-necessary | 11 months | This cookie is set by GDPR Cookie Consent plugin. The cookies is used to store the user consent for the cookies in the category "Necessary". |
cookielawinfo-checkbox-others | 11 months | This cookie is set by GDPR Cookie Consent plugin. The cookie is used to store the user consent for the cookies in the category "Other. |
cookielawinfo-checkbox-performance | 11 months | This cookie is set by GDPR Cookie Consent plugin. The cookie is used to store the user consent for the cookies in the category "Performance". |
CookieLawInfoConsent | 1 year | Records the default button state of the corresponding category & the status of CCPA. It works only in coordination with the primary cookie. |
PHPSESSID | session | This cookie is native to PHP applications. The cookie is used to store and identify a users' unique session ID for the purpose of managing user session on the website. The cookie is a session cookies and is deleted when all the browser windows are closed. |
viewed_cookie_policy | 11 months | The cookie is set by the GDPR Cookie Consent plugin and is used to store whether or not user has consented to the use of cookies. It does not store any personal data. |
Cookie | Duration | Description |
---|---|---|
CONSENT | 2 years | YouTube sets this cookie via embedded youtube-videos and registers anonymous statistical data. |
_ga | 2 years | The _ga cookie, installed by Google Analytics, calculates visitor, session and campaign data and also keeps track of site usage for the site's analytics report. The cookie stores information anonymously and assigns a randomly generated number to recognize unique visitors. |
_gat_UA-48954022-1 | 1 minute | A variation of the _gat cookie set by Google Analytics and Google Tag Manager to allow website owners to track visitor behaviour and measure site performance. The pattern element in the name contains the unique identity number of the account or website it relates to. |
_gid | 1 day | Installed by Google Analytics, _gid cookie stores information on how visitors use a website, while also creating an analytics report of the website's performance. Some of the data that are collected include the number of visitors, their source, and the pages they visit anonymously. |
Cookie | Duration | Description |
---|---|---|
VISITOR_INFO1_LIVE | 5 months 27 days | A cookie set by YouTube to measure bandwidth that determines whether the user gets the new or old player interface. |
YSC | session | YSC cookie is set by Youtube and is used to track the views of embedded videos on Youtube pages. |
yt-remote-connected-devices | never | YouTube sets this cookie to store the video preferences of the user using embedded YouTube video. |
yt-remote-device-id | never | YouTube sets this cookie to store the video preferences of the user using embedded YouTube video. |