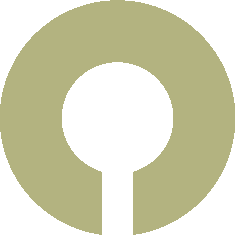
Production Control
If your current production control system is stand-alone, inflexible, too limited for the job, lacks workflow and clear status, then now is the time to consider moving to the FMIS Production Control system.
Functionally rich yet simple to use
The key to efficient production and assembly lies in the flexibility of bill of materials within the product and parts set-up. The set-up of production drivers and details can be an extremely laborious task but FMIS provides mass import facilities for all your production details. The loaded production assemblies can detail all the routing, purchasing, production and stock consumption rules as you turn raw materials into finished goods or assemble kits for sales.
Resource management
The minimum stock levels for raw materials and sub-assembly, combined with the demand from sales orders for finished goods, creates a demand/time profile within Production Control. The auto-replenishment process provides you with a flexible means of generating purchase orders, sub-assembly or finished goods based upon the overall sales or estimated demand. Production orders will provide sufficient information to deal with all of your routing, quality assurance and authorisation workflows. You can issue finished goods back to stock automatically or by allocating serialised items. Production Control can automate much of this process even across a complex bill of materials resulting in significant savings in time and preparation.
Key features
- Multi-company
- Multi-lingual
- Customisable workflows
- Electronic authorisation
- Complex bill of materials at all levels
- Full part version control
- Full engineering attachments and cad drawings linked or uploaded
- Clear distinction between raw materials, sub-assemblies and finished goods
- Material management through time based auto-replenishment
- Phantom bill of materials (BOM) provides additional flexibility
- Detailed and customisable production work order documentation
- Workflow routing for production work orders
- Manual or auto allocation of raw materials and sub-assemblies
- Customisable pick lists and put away documents
- Work in process (WIP) accounting
- Stock accounting
- Finished goods and despatch accounting
- Resource management
Production assembly definitions
- Multi-level bill of materials easily constructed, copied and uploaded from a spreadsheet
- HSE and government quality control attributes recorded and tracked
- Copy bill of materials
- Version control
- Full pricing and standard costing
Demand management
- Receive demand from quotes or sales orders
- Revise demand profile with future forecasted quotes
- Use requisitions to issue stock to internal use and balance sheet treatment as required
Materials planning
- Use the auto-replenishment date based ranges to produce the optimised just in time purchase and production work orders
- Provide clear visibility of current and future stock positions based on changes to demand profiles
Automated demand fulfilment
- Utilise minimum stock levels and quantity re-order levels to automatically generate mass purchase orders to preferred or specified vendors using the latest possible order date
- Latest re-order dates automatically calculated based on the critical path in the routing and minimum lead time
- Produce mass production orders using just in time principles and simplified by using phantom bill of materials
Automated control
- Workflow routing for production work orders
- Auto allocation of bulk stock to materials demand for production work orders
- Manual selection or auto allocation of serialised raw materials and sub–assembly
- Customisable pick lists
- Controlled stock allocation from raw material or sub-assembly to work in progress
- Auto or manual allocation of serial numbers as finished goods are booked back into stock
- Production control reporting and pipeline analysis
Reporting
- All documents easily customisable
- Base reports can be cloned, modified and customer specific
- Base reports can be linked to particular workflows
- Dashboards and business intelligence
FAQ
What types of production processes can FMIS Production Control manage?
FMIS Production Control is designed to handle a wide range of production processes, including discrete manufacturing, assembly, and kitting operations.
Can the software handle complex Bill of Materials (BOM)?
Yes, it supports multi-level BOMs, allowing for detailed and intricate production assemblies.
How does the auto-replenishment feature work?
The auto-replenishment feature uses time-based ranges to optimise just-in-time purchasing and production orders, ensuring materials are available when needed without overstocking.
Can we manage demand from sales orders and forecasts?
Yes, the software allows you to receive demand from quotes or sales orders and adjust demand profiles based on future forecasts.
Who can benefit from FMIS Production Control?
FMIS Production Control is ideal for project-based manufacturers needing project cost tracking and process control. It suits industries like engineering, aerospace, and specialist manufacturing.
Is training provided for the users?
Yes, FMIS offers training to enable your team can use the system effectively, maximising its value.
How does FMIS ensure data security within the system?
FMIS follows industry best practices for data security, including encryption, role-based access control, and secure system integrations.
How much does FMIS Software cost?
Pricing depends on factors like the number of users, required modules, and deployment method. Contact us to discuss your needs and request a personalised quote using our contact form.